Tongxiang Qianglong Machinery Co., Ltd. is high-tech China wholesale computerized flat knitting machine manufacturers, specialized in designing, developing, and manufacturing Knitting Machinery..
3D knitting and traditional manufacturing methods each have their own strengths and weaknesses. Here's a comparison of the two approaches:
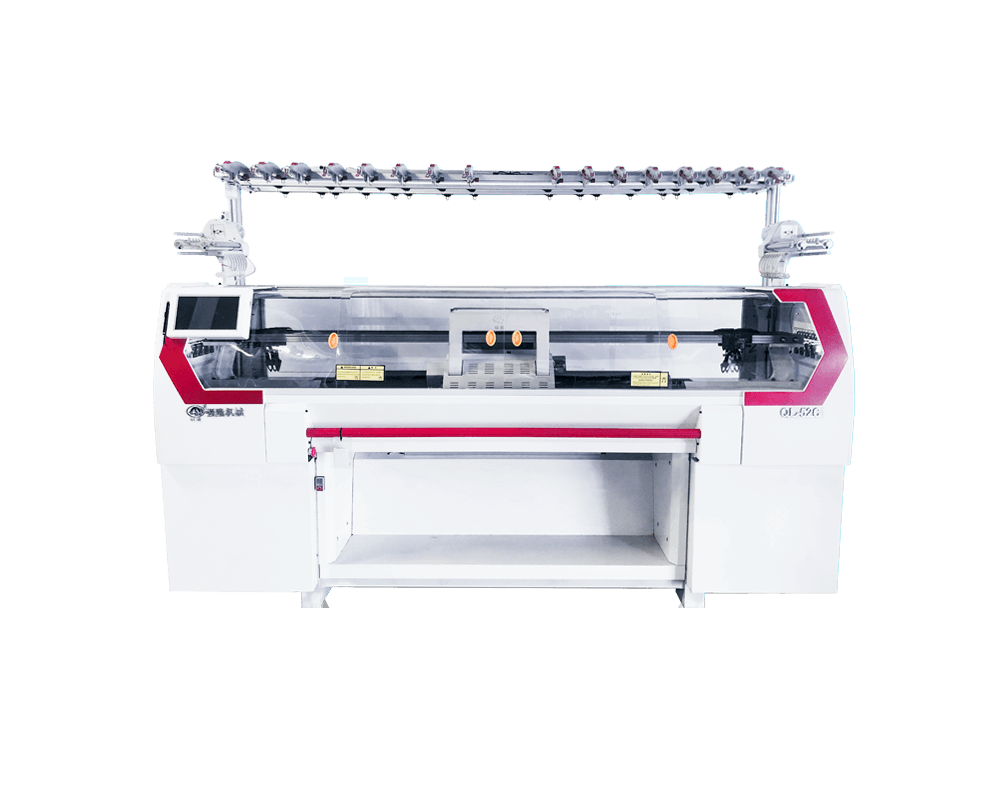
3D Knitting:
Advantages:
Customization: 3D knitting enables high degrees of customization, allowing designers to create intricate patterns, textures, and even personalized products easily.
Seamlessness: Many 3D knitting techniques produce seamless garments or structures, eliminating the need for labor-intensive sewing and reducing potential points of weakness.
Reduced Waste: 3D knitting can minimize material waste by directly producing the desired shape, which can be especially advantageous when working with expensive or specialty materials.
Complex Structures: 3D knitting machines can create complex 3D structures that are challenging to achieve with traditional flat knitting or weaving methods.
Rapid Prototyping: Prototyping and sampling are often quicker with 3D knitting since adjustments to patterns can be made digitally before production.
Localized Production: 3D knitting can be decentralized, allowing for local or on-demand production, reducing shipping distances and associated carbon footprint.
Challenges:
Learning Curve: Working with 3D knitting machines and designing patterns requires familiarity with digital design tools and the machine's programming.
Material Limitations: Not all materials are suitable for 3D knitting, and machine compatibility can vary based on the fibers and yarns being used.
Machine Cost: Initial investment in 3D knitting machines and related technology can be high, making it potentially less accessible for small businesses.
Traditional Manufacturing Methods (e.g., Sewing, Weaving, Flat Knitting):
Advantages:
Versatility: Traditional methods can work with a wide range of materials, from delicate fabrics to heavy textiles.
Experience: Skilled artisans with experience in sewing, weaving, or knitting can produce high-quality items with attention to detail.
Low Initial Investment: Traditional methods often require less capital investment compared to acquiring high-tech 3D knitting machinery.
Material Variety: A broader variety of material types can be integrated into traditional manufacturing methods.
Challenges:
Complexity: Complex designs and structures may be more challenging and time-consuming to produce using traditional methods.
Waste Generation: Traditional methods can generate more waste due to the need for cutting and sewing multiple pieces together.
Limited Customization: Achieving intricate, customized designs and patterns might require more manual effort and skilled labor.
Speed: Traditional methods can be slower, especially for larger quantities, due to the sequential nature of processes like sewing or weaving.
Seams and Weak Points: Seams and joins can create potential weak points in the final product, affecting durability.
The choice between 3D knitting and traditional manufacturing methods depends on factors like the specific application, desired customization level, production volume, material requirements, and available resources. In some cases, a hybrid approach that combines the strengths of both methods might be the most suitable solution.
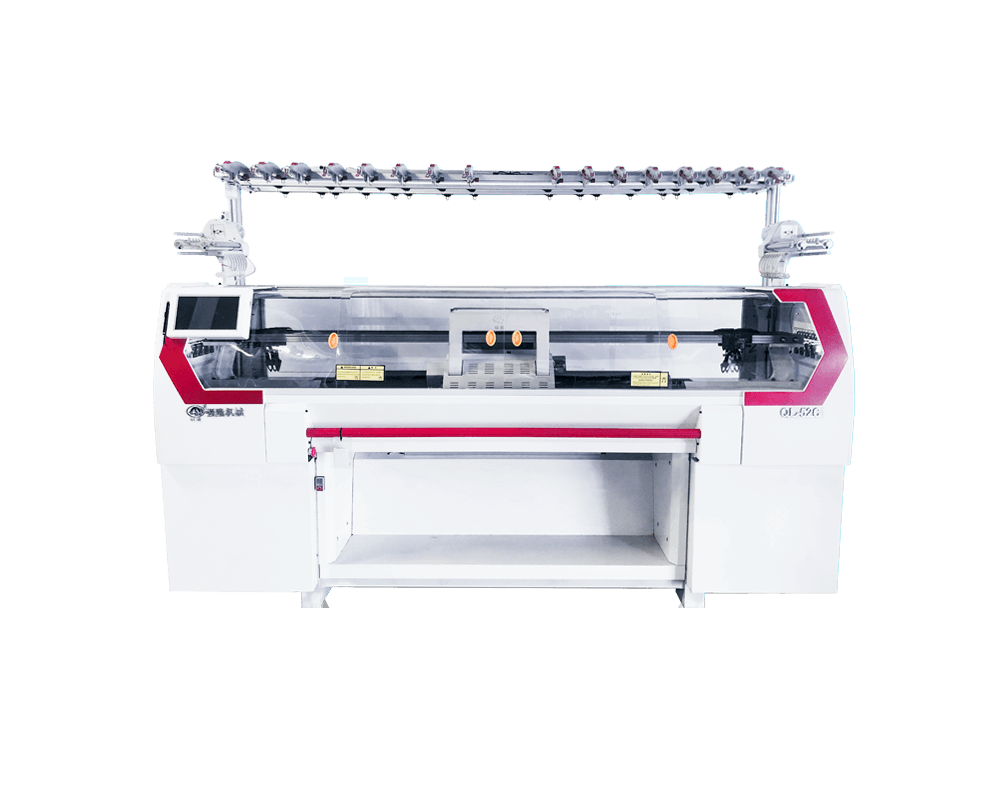
3D Knitting:
Advantages:
Customization: 3D knitting enables high degrees of customization, allowing designers to create intricate patterns, textures, and even personalized products easily.
Seamlessness: Many 3D knitting techniques produce seamless garments or structures, eliminating the need for labor-intensive sewing and reducing potential points of weakness.
Reduced Waste: 3D knitting can minimize material waste by directly producing the desired shape, which can be especially advantageous when working with expensive or specialty materials.
Complex Structures: 3D knitting machines can create complex 3D structures that are challenging to achieve with traditional flat knitting or weaving methods.
Rapid Prototyping: Prototyping and sampling are often quicker with 3D knitting since adjustments to patterns can be made digitally before production.
Localized Production: 3D knitting can be decentralized, allowing for local or on-demand production, reducing shipping distances and associated carbon footprint.
Challenges:
Learning Curve: Working with 3D knitting machines and designing patterns requires familiarity with digital design tools and the machine's programming.
Material Limitations: Not all materials are suitable for 3D knitting, and machine compatibility can vary based on the fibers and yarns being used.
Machine Cost: Initial investment in 3D knitting machines and related technology can be high, making it potentially less accessible for small businesses.
Traditional Manufacturing Methods (e.g., Sewing, Weaving, Flat Knitting):
Advantages:
Versatility: Traditional methods can work with a wide range of materials, from delicate fabrics to heavy textiles.
Experience: Skilled artisans with experience in sewing, weaving, or knitting can produce high-quality items with attention to detail.
Low Initial Investment: Traditional methods often require less capital investment compared to acquiring high-tech 3D knitting machinery.
Material Variety: A broader variety of material types can be integrated into traditional manufacturing methods.
Challenges:
Complexity: Complex designs and structures may be more challenging and time-consuming to produce using traditional methods.
Waste Generation: Traditional methods can generate more waste due to the need for cutting and sewing multiple pieces together.
Limited Customization: Achieving intricate, customized designs and patterns might require more manual effort and skilled labor.
Speed: Traditional methods can be slower, especially for larger quantities, due to the sequential nature of processes like sewing or weaving.
Seams and Weak Points: Seams and joins can create potential weak points in the final product, affecting durability.
The choice between 3D knitting and traditional manufacturing methods depends on factors like the specific application, desired customization level, production volume, material requirements, and available resources. In some cases, a hybrid approach that combines the strengths of both methods might be the most suitable solution.