Tongxiang Qianglong Machinery Co., Ltd. is high-tech China wholesale computerized flat knitting machine manufacturers, specialized in designing, developing, and manufacturing Knitting Machinery..
Maintenance and troubleshooting are essential aspects of ensuring the optimal performance of computerized flat knitting machines. Proper care and timely resolution of issues contribute to the longevity and efficiency of these machines. Here's an overview of how maintenance and troubleshooting typically work:
Maintenance:
Routine Inspection:
Regularly inspect the machine for any signs of wear, loose components, or damage. This includes checking needles, yarn feeders, belts, and other mechanical parts.
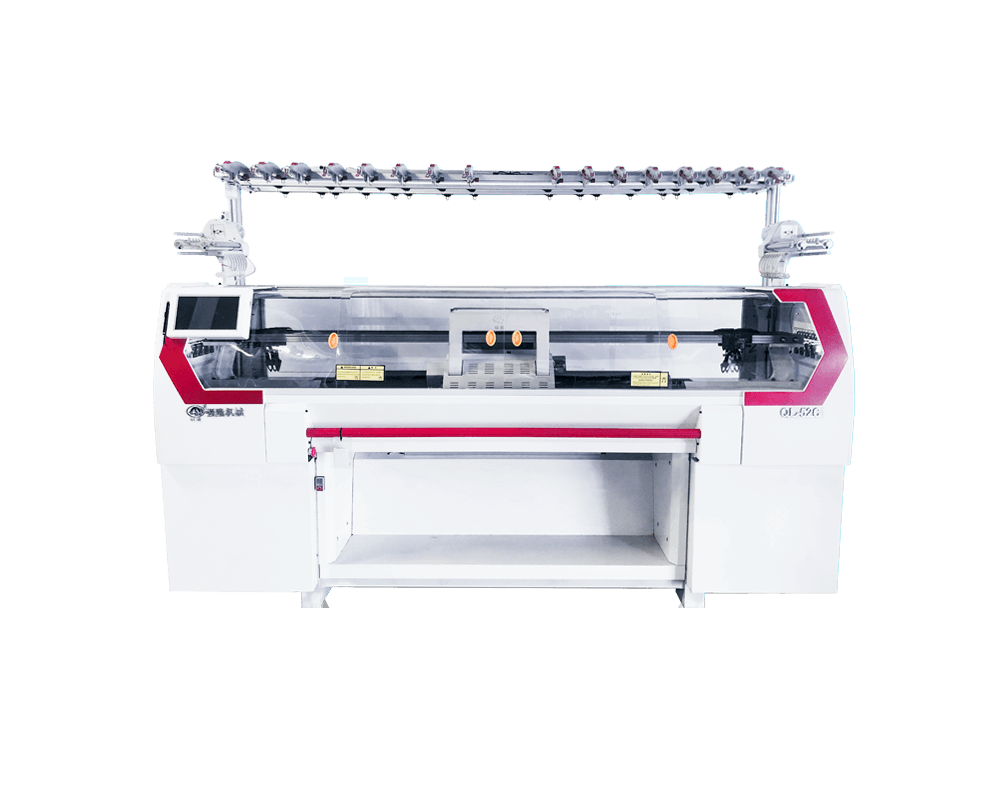
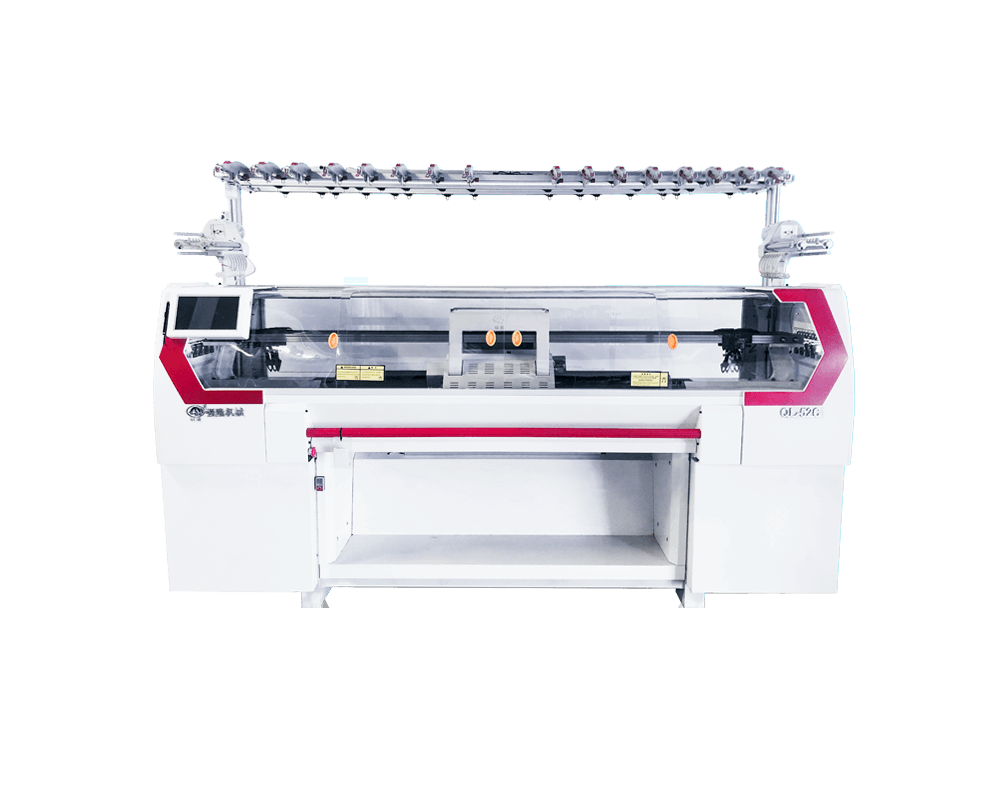
Cleaning:
Keep the machine clean from dust, lint, and other debris that may accumulate during operation. Clean and lubricate moving parts as recommended by the manufacturer.
Yarn Path Inspection:
Check the yarn paths to ensure that there are no obstructions or tangled yarn that could impede the feeding process.
Needle Maintenance:
Inspect and replace needles as needed. Damaged or bent needles can affect the quality of the knit fabric.
Software Updates:
Stay updated with the latest software releases and firmware updates provided by the manufacturer. Software updates may include improvements, bug fixes, and new features.
Calibration:
Periodically calibrate the machine to ensure accurate needle selection and stitch formation. Calibration may be necessary after significant machine usage or changes in environmental conditions.
Troubleshooting:
Error Messages:
The machine's control system often provides error messages or codes that indicate specific issues. Operators should refer to the machine's manual to interpret these messages and identify the corresponding troubleshooting steps.
Diagnostic Tools:
Some computerized flat knitting machines are equipped with diagnostic tools that can help identify and isolate problems. These tools may include self-check routines or diagnostic modes that provide additional information about the machine's status.
Pattern or Design Issues:
If there are issues with the knit fabric not matching the digital pattern, operators should review the design file for errors. Check for issues such as incorrect stitch counts, color changes, or pattern instructions.
Yarn Feed Problems:
If the machine experiences yarn feed problems, operators should inspect the yarn feeders, tensioners, and guides. Ensure that the yarn paths are clear and that yarn is properly loaded.
Needle Selection Issues:
Problems with needle selection may affect the knit pattern. Check for stuck or malfunctioning needles, and verify that the needle selection mechanisms are functioning correctly.
Sensor Calibration:
If the machine uses sensors for various functions, such as detecting yarn breaks or needle positions, calibration may be necessary to ensure accurate readings.
Technical Support:
In cases where troubleshooting becomes challenging, reaching out to the manufacturer's technical support or service team for assistance is crucial. They may provide guidance over the phone, through remote diagnostics, or on-site support.