Tongxiang Qianglong Machinery Co., Ltd. is high-tech China wholesale computerized flat knitting machine manufacturers, specialized in designing, developing, and manufacturing Knitting Machinery..
The environmental friendliness of the production process of 3D Flyknit compared to traditional methods depends on various factors, including the specific technologies used, materials employed, and the overall life cycle of the products. Here are some considerations:
Advantages of 3D Flyknit Technology:
Reduced Waste: One of the environmental benefits of 3D Flyknit technology is the potential for reduced waste. Traditional cut-and-sew methods often generate more material waste due to the need for pattern cutting and stitching. 3D Flyknit machines can create seamless garments, minimizing the amount of material discarded.
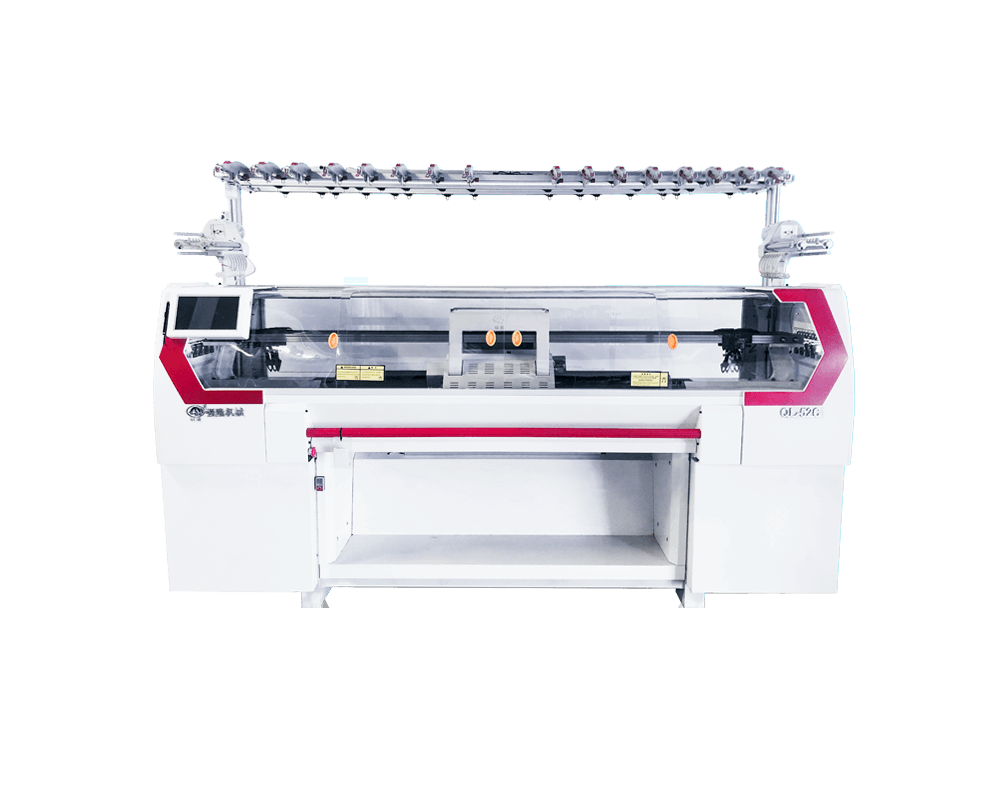
Energy Efficiency: Some 3D Flyknit machines are designed to be energy-efficient. The automation and digital control of the knitting process may contribute to optimized energy usage compared to certain traditional manufacturing methods.
Customization and Localized Production: 3D Flyknit technology allows for customization and on-demand production, reducing the need for large-scale, mass production. This can help minimize overproduction and excess inventory, leading to a more sustainable production model.
Lightweight and Resource-Efficient Designs: The ability to create lightweight and breathable fabrics with 3D Flyknit technology can contribute to resource efficiency. Lightweight textiles often require fewer raw materials, and they may also lead to more energy-efficient transportation.
Considerations and Challenges:
Material Selection: The environmental impact of 3D Flyknit production depends on the materials used. While the technology is versatile and can work with various fibers, the environmental footprint varies based on the sustainability of the chosen materials.
Chemical Usage: Some 3D Flyknit processes may involve the use of chemicals in the treatment of fibers. The environmental impact of these chemicals should be considered, and efforts can be made to use eco-friendly treatments.
End-of-Life Considerations: The sustainability of textiles goes beyond the production phase. Consideration should be given to the end-of-life stage, including recyclability and biodegradability of the materials used.
Equipment Manufacturing: The production of the 3D Flyknit machines themselves involves the extraction of raw materials and manufacturing processes. Assessing the environmental impact of the production of these machines is also important.
Comparison with Traditional Methods:
Waste Reduction: Compared to traditional methods that involve cutting and sewing patterns, 3D Flyknit technology has the potential to significantly reduce fabric waste.
Efficiency in Small Batches: Traditional methods may have challenges in efficiently producing small batches or custom orders, leading to overproduction. 3D Flyknit's customization capabilities can address this issue.
Transportation Impact: The weight and volume of traditional textile products can contribute to higher transportation costs and emissions. Lightweight 3D Flyknit textiles may have an advantage in this regard.
While 3D Flyknit technology offers environmental advantages in certain aspects of production, it is crucial to assess the entire life cycle and specific practices of individual manufacturers to make a comprehensive comparison with traditional methods.
Sustainable material choices, energy efficiency, and responsible end-of-life considerations play key roles in determining the overall environmental impact.